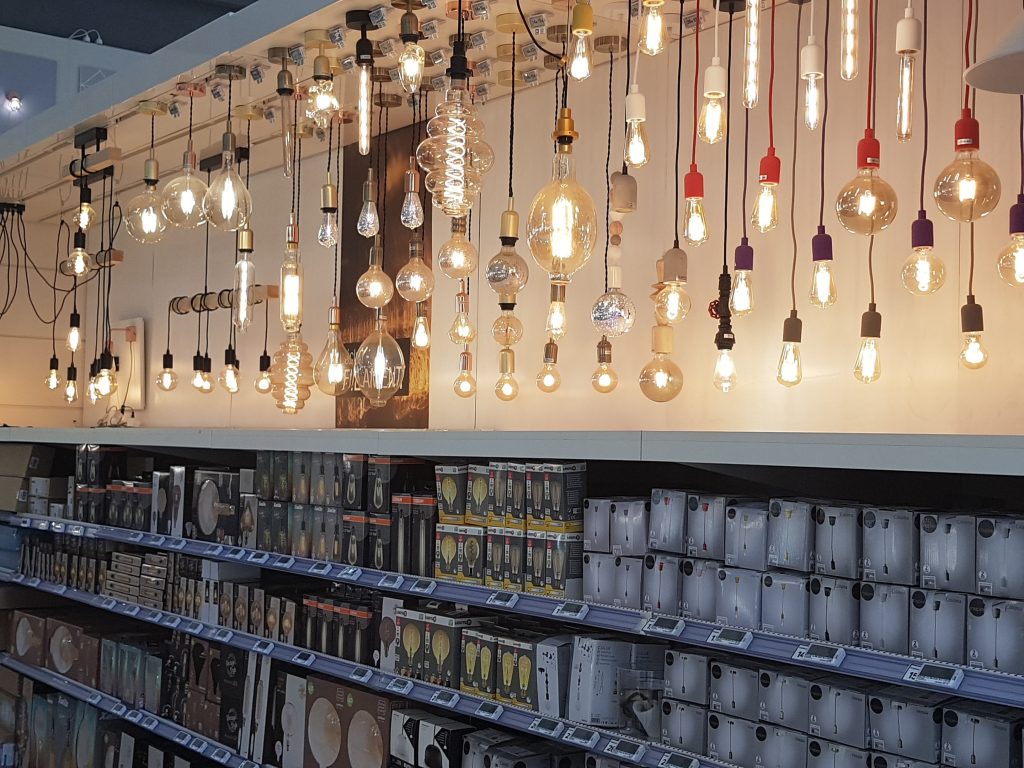
Inventory management: definition and issues
The acquisition and storage of inventory represents a significant cost to businesses. This is why it is essential to ensure the sustainability of the company, to have good inventory management. To do this, the company must determine:
- when to stock up
- quantities to buy
This management is essential to meet all customer requests.
Avoid under-storage
If the stock is not large enough, we are talking about stock outages or undersupery. If the company has a product not available at a sale, a stock outage has a negative impact on the service rate. This can result in a loss of the company’s customers and buyers, who turn to competition.
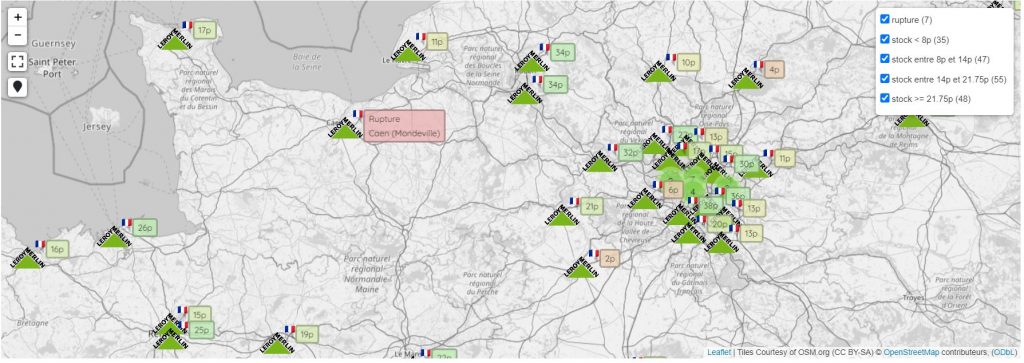
Avoid overstocking
Maintaining too high a level of products entails very high costs (Logistics, fixed assets …) that weigh heavily in operating accounts. In addition, poorly controlled volumes create a risk of becoming obsolete or aging poorly.
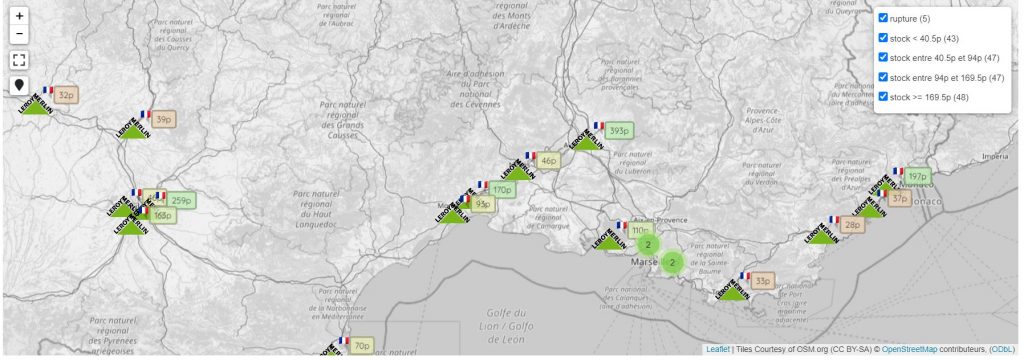
How do you manage your inventory?
Safety and alert threshold.
Safety threshold (SS): it aims to avoid stock outage. It is a minimum amount to hold to meet demand. When the safety threshold is reached, the command point is triggered if no Alert Threshold (SA) is set. To be effective, the security threshold must take into account resupply times. The longer the delay, the higher the security stock and vice versa.
Warning threshold (SA): it is the stock that triggers the order, it is equal to minimum stock – security stock. Minimum stock (SM): it is the stock that corresponds to sales during delivery times. For example, a supplier asks for a week of delivery. If the sales of an item are 20 pieces per week, that is the minimum stock. If the store orders with only 15 pieces left, it will be out of stock before the end of the week.
The distribution of your stocks …
To better track your stored products, Retail Shake geolocates your inventory. You can see on the map, those that are present in each store. To get better visibility, you can filter according to your needs (product breaking or less than such number of parts).
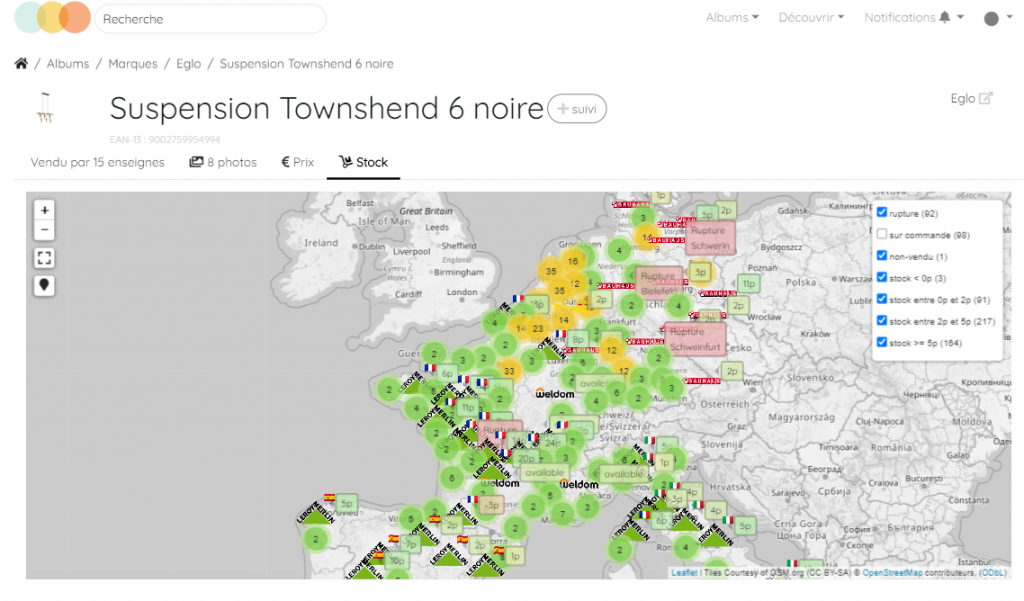
You are alerted in real time to the quantity and value of your inventory as well as the stores that are out of order. This information is indicated for each product.
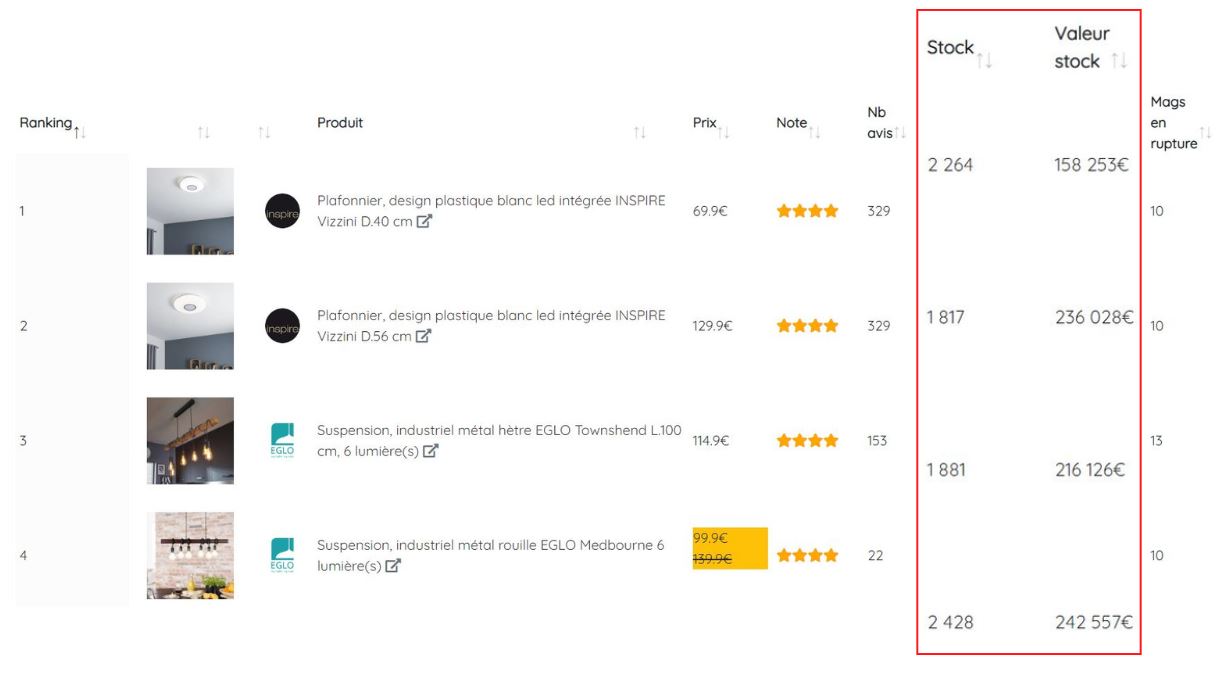
Retail Shake helps you locate your inventory, detect any breaks or those that are left. You are then master in your decisions: delivery arbitrages, stock balances in a geographical area, destocking or reverse logistics.
To find out where your products are distributed, we invite you to read this article: But where are your products?!?